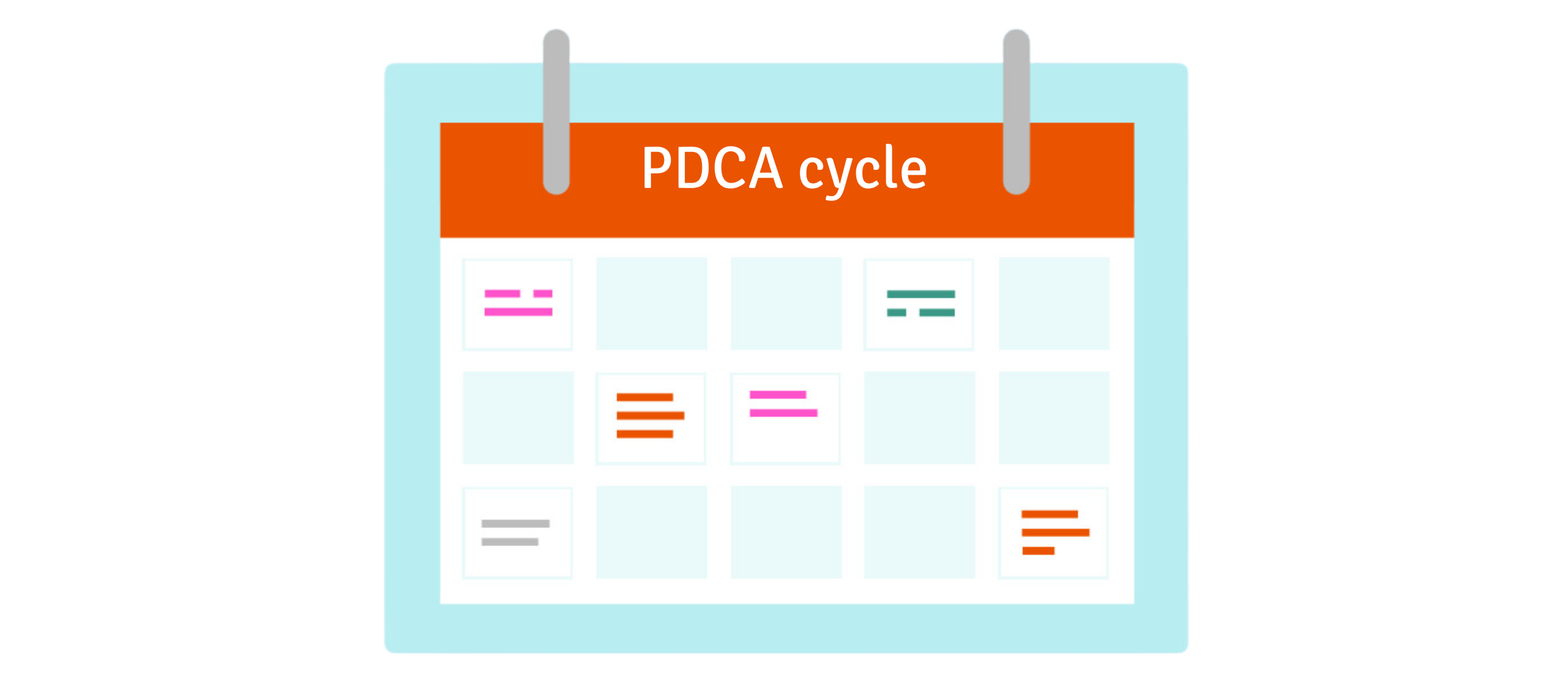
What is a PDCA cycle?
Master Your Purpose. Own Your Freedom. With ICR.
Using Deming's PDCA cycle, which stands for Plan Do Check Act, continuous process improvement is the foundation for implementing the periodic management cycle. This approach allows you to monitor whether you are on track to achieve your long-term plan while simultaneously implementing improvements in processes.
PLAN - PLANNING
First, you analyze how the current tasks in the process are being carried out. Next, you design a plan to adjust these tasks to lead to process improvements. Finally, you set objectives for these improvements to ensure they are measurable.
DO - IMPLEMENTATION
You implement the planned process improvements.
CHECK - CONTROL
You verify whether everything has gone according to plan by measuring the results of the process improvements. You compare these results with the original situation and check if they meet the objectives of the process improvements.
ACT - ADJUSTMENT
From the previous step, you identify what did not go according to plan. Therefore, you adjust the process to address these identified deviations.
In the PDCA cycle, the executive management is responsible for the highest level at which processes are managed. The management bridges the gap between the highest level and the employee level. The core of the PDCA cycle is that, in principle, every employee and participant in a process is able to assess and improve their own way of working. After all, the actions of the employee are ultimately a derived (partial) process of the highest level.
The PDCA cycle encourages organizations to continuously strive for the improvement of processes, products, and services. By regularly planning, implementing, checking, and adjusting, organizations can gradually improve their performance. Additionally, they can identify and correct inefficiencies in their processes. This can lead to increased productivity, reduced waste of resources, and cost savings.
The process of checking and adjusting in the PDCA cycle also helps your organization ensure the quality of products and services. By regularly evaluating and implementing improvements, your organization increases the chances of meeting or even exceeding customer expectations. This also strongly promotes the maintenance of quality standards.
By systematically planning and checking, your organization can identify potential risks and implement ways to mitigate them. This helps minimize risks and makes business activities more resilient to unforeseen events. The PDCA cycle also provides your organization with a structured framework for decision-making. By collecting, analyzing data, and taking action based on it, your organization makes well-informed decisions that are based on facts and results.
Thus, the PDCA cycle offers your organization a highly effective methodology for improving processes, ensuring quality, managing risks, and making better decisions. All of this ultimately contributes significantly to competitiveness and success.
Sustainable success through controlled and manageable growth
The ICR Growth & Success SaaS Platform helps people and organizations find balance and peace, through controlled and manageable growth, with the aim of a healthy and sustainably successful organization. We do this through the all-encompassing ICR Cycle.
Being inControl in this process from ambition to result is crucial. Within the ICR Cycle, inControl actually means controlled and manageable growth. The dashboard gives you insight into the current status. In the video below you can see how the dashboard transforms from the moment you start using ICR.
With our 4 ICR subscription options, you can decide for yourself when to fully engage with the entire ICR Cycle. Choose our successful approach and start your process 'from ambition to result' with the more than affordable ICR Ambition Refresher subscription.
General applications of the ICR Growth & Success SaaS Platform
The ICR Growth & Success SaaS Platform addresses a wide range of business needs, making it a versatile tool for organizations striving for sustainable success. Below is an overview of its general applications, along with the added value it provides for businesses and organizations.
Learn more about the general applications of the ICR Growth & Success SaaS platform.